Learn the 8 "hidden" wastes you should avoid to maximize your organization's efficiency and profit margins.
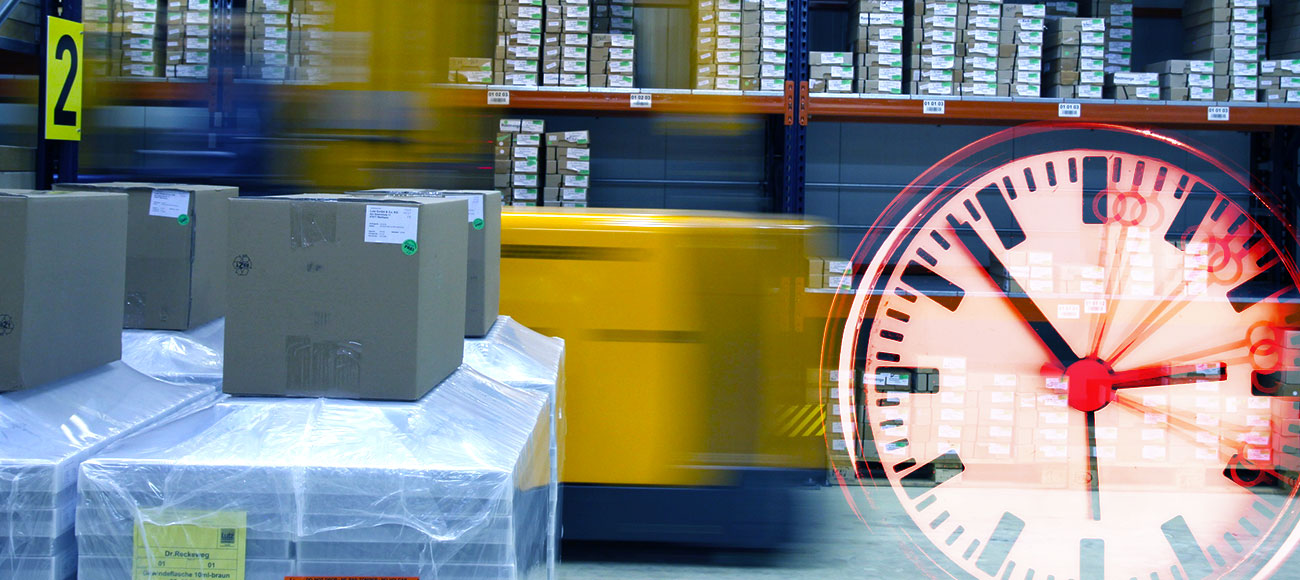
Waste exists in every company and it is each company’s responsibility to eliminate it. No matter the industry, waste decreases efficiency while increasing lead times and process costs. When a company reduces its non-value-added wastes, it increases profit margins and reduces production and process times.
The original seven "Wastes of Lean" were first introduced by Toyota (then called Toyoda) in the 1970’s when Taiichi Ohno was creating the Toyoda Production System (TPS). Ohno observed non-value-added steps in the work process that he referred to as muda (waste). He further expanded on waste by explaining that there are actually two types of waste, which are:
- Type I Waste - Non-value-added activity, necessary for end customer
- Type II Waste - Non-value-added activity, unnecessary for the end customer
Type I waste is necessary for the business but a non-value-added steps in the process to the customer. These steps must be accomplished even though there is no direct value added to the final product or service. Type I wastes include: finance reporting, legal paperwork, reports, quality assurance testing, etc.
Type II wastes are unnecessary to the customer and therefore should be eliminated from the process. The original 7 unnecessary wastes Taiichi Ohno conceptualized- Transportation, Inventory, Motion, Waiting, Overprocessing, Overproducing, and Defects- came from this category and can be easily remembered by the acronym TIMWOOD.
What is Waste
Waste is any action in a process that does not add value to the customer. All actions in a process should provide value to the customer and be something the customer is willing to pay for. The best way to evaluate if a step in your process is a value added or non-value-added is to pick an activity and stop doing it. Would the customer (either internal or external) know? If they do not, then this step is most likely a non-value-added step and should be removed from the process.
The best way to evaluate if a step in your process is a value added or non-value-added is to pick an activity and stop doing it. Would the customer know?
The Benefits of Eliminating Waste
By eliminating waste in the workplace, your company will:
- Reduce cost of poor quality
- Improved process efficiency
- Increase profit margins
- Reduce inventory
- Improved employee productivity
How To Remove Waste
The most effective way to remove waste is to conduct a Six Sigma project which uses statistical data to offer solutions to improve your process. The goal of a Six Sigma project is to increased customer satisfaction and improve process performance by removing variability and waste reduction. The results of having a more streamlined process is consistently producing high quality products that meet customer expectations.
If you do not wish you use a statistically analysis methodologies, you can use other Lean tools such as 5S and Kaizen to make improvements to your facility. 5S is based on 5 steps that will increase the organization and efficiency of your facility. The 5 steps are: Sort, Set in Order, Shine, Standardize, and Sustain. Kaizen is a Japanese word that translated to continuous incremental improvements and when implemented in a company can have an impact of company culture and process improvement.
The 8 Wastes of Lean
Waste | Description |
---|---|
Transportation | Movement of items, materials or information unnecessarily from one place to another |
Inventory | Any excess inventory; raw materials, work in process or finished goods |
Motion | Unnecessary movement by people or equipment (bending, walking, climbing) |
Waiting | Any delay or inactive time due to an incompletion in another step of the process |
Overprocessing | Unnecessary steps or too many steps in a process |
Overproducing | Producing more finished good than the customer requires |
Defects | Finished goods that fail to meet specifications set forth by customer requirements |
Unused Skills | Unused employee talents and creativity |
1. Transportation
Any unnecessary movement of people, materials, inventory or information from one place to another. The actual step of transportation provides no added value to the product or customer. This step increases the probability of product damage during unnecessary transportation and adds additional time to the process of delivering the final product.
Investigate time and cost-efficient methods of moving products through the production flow or from one plant to another. Using Lean tools like floor plans or a process flowchart can help you visually map out the most efficient process for your company. With a more efficient process your company can decrease time spent handling materials, damage probability during travel, training time and many other variables that go into the transportation of products.
2. Inventory
Simply put, inventory adds no direct value to the customer. Inventory can refer to any raw materials, work in progress materials or finished goods sitting on racks. The “waste” in this step comes from excess inventory through any stage of the process that is more than the customer requires. Excess inventory is a direct waste to financial, production and storage resources. Also, the excess inventory is at risk to be damaged, spoiled, and hide potential quality issues.
Some of the most effectives tools to help you control your inventory are:
- Value Streams
- SIPOC Diagram
- Just-in-Time (JIT) Manufacturing
- Kanban System
Using these and other Lean tools you can evaluate your inventory to see if you’re carrying excess and make data driven adjustments.
3. Motion
Any movement in a process by a person, equipment or information that does not add value to the customer is considered wasteful. Any time spent searching, walking, bending, reaching, twisting and lifting are all associated to wasted movement. Most often these wasted movements are due to issues in the production layout and general organization within the workspace. Ideally, your facility should be set up so there is a consistent flow throughout the production process, all tools and materials needed for a task are close by, and tools are easily identifiable. One of the most effective tools to help understand the movement of a person or materials in a process is to use a Spaghetti Diagram.
4. Waiting
Any time there is a delay, or a person is waiting on other steps of the process so they can complete their tasks. Anytime one task takes longer than another the result will be someone standing around not being as productive as possible. There are multiple reasons why the delay has been caused ranging from:
- Inefficient process flow
- Shortage of materials
- Insufficient equipment
- Employee needs instructions
- Unbalanced workload
5. Overprocessing
Having too many steps in a process or exceeding customer requirements. The goal of the company should be to condense work-in-process (WIP) time and maximize the production possibility. The time and money wasted on unnecessary steps could be better spent completing value added steps that the customer is willing to pay for. Some examples of over processing include excessive packaging, over-engineering, adding features that will not be used, and marking unused areas of a facility.
The first step to correcting over processing is knowing the Voice of the Customer (VOC). Collect feedback from your customers so to understand their quality acceptance standards and use that information to create best practices in your facility to constantly meet the customers standards.
6. Overproducing
Producing too much too soon! This is one of the most serious mistakes that companies make in their production process because it can cause other wastes like inventory costs, wasted material, wasted manpower, lack of storage space, excess capital allocated to inventory sitting on shelves... and the list goes on. It is essential for your company to understand when and how much product the customer typically purchases. Once your company understands your customers' purchasing habits, you can create internal processes that help regulate fast moving products.
By understanding the customer’s demands, the benchmark for how much of a product your company should produce and any production that exceeds that number is waste. Creating an influx of unneeded product can lead to other non-value-added wastes.
7. Defects
Defects refers to any corrections or repairs that must be made to a product because it failed to meet customer expectation. The overall goal of the production environment should be to get it done right the first time. In Six Sigma, quality success at the highest level is defined as your processes resulting in 3.4 or less defects per million opportunities. Defective products that need to be reworked or scrapped add additional cost to the process and provide no value to the customer.
Simply put, to reduce the number of defects, implement a more efficient production system. Using methodologies such as DMAIC (Define, Measure, Analyze, Improve, Control) or PDCA (Plan-Do-Check-Act) will help you focus your efforts on areas that cause the most defects. These methodologies are designed to eliminate defects in process, improve quality, and standardize the work to deliver consistent results.
Employees can be a company’s most valuable resources to ensure the success of business.
8. Unused Skills
More recently, an 8th waste of lean has emerged- the unused skills and creativity of employees. Another commonly used term is latent skills, which is where an employee does not currently have the skills but shows potential to learn. Unfortunately, companies across all markets are failing to place their employees in the proper areas or implementing training programs that are not effectively teaching the information.
Employees can be a company’s most valuable resources to ensure the success of business. On the other hand, a company can become stagnant and even decline when employees are not properly trained, respected or motivated.
Take the approach of maximizing your employees' natural and underutilized talents. Instead of micromanaging, encourage employees to take ownership of their department, area, process, etc. Ask your employees how processes can be improved-- after all they’re the ones doing the work, day in and day out.
Free eBook: How To Create a 5S Culture
Learn how to implement 5S with our free 5S Guide. Download now.